What is The Packaging Process for Bottled Chewing Gum?
2023-10-11
What is The Packaging Process for Bottled Chewing Gum?
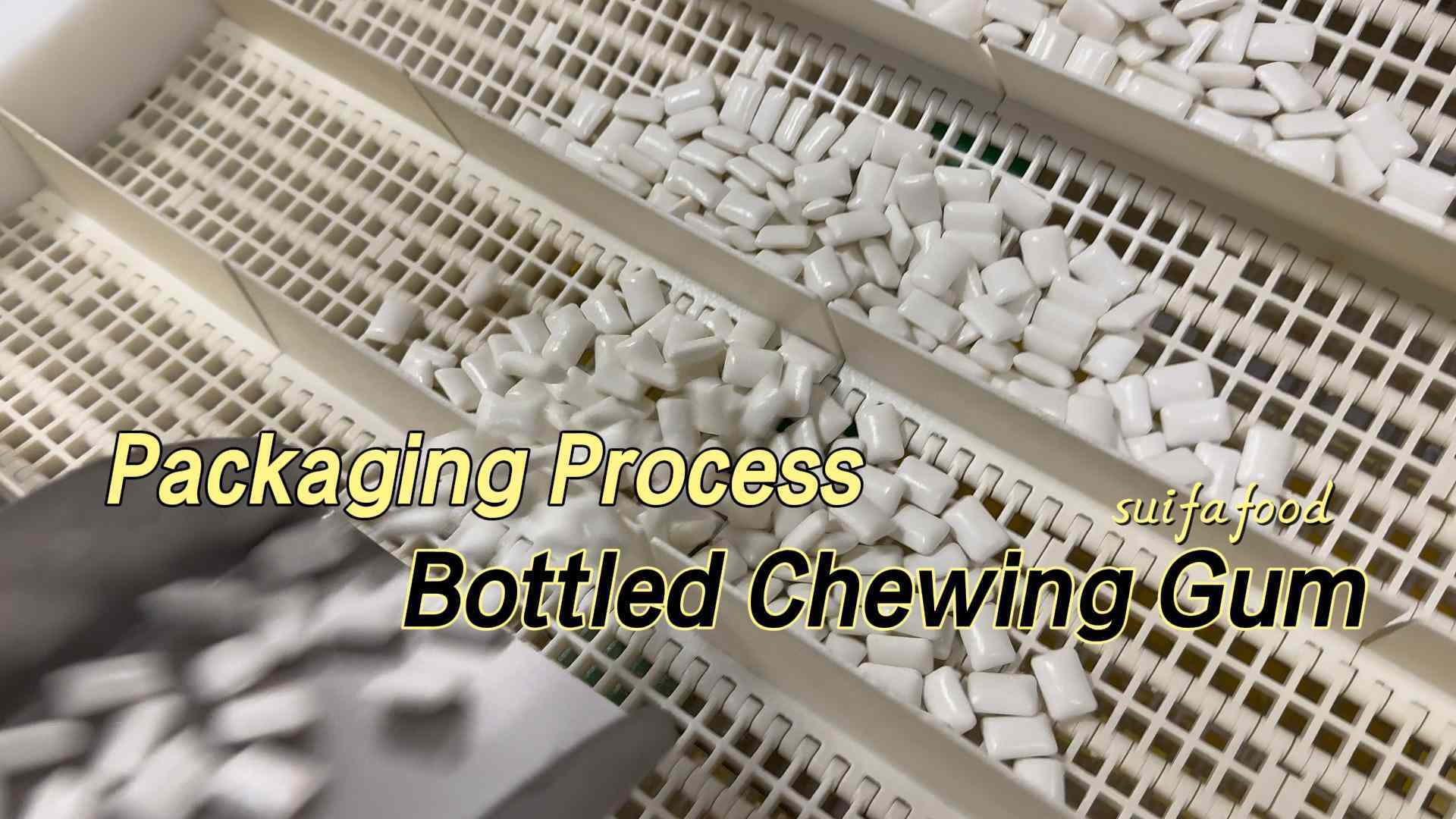
As a business owner, ensuring that your product looks as appealing as it tastes can make or break the consumer's first impression. In the confectionery industry, this is especially important when considering the packaging process for a delicate product like chewing gum. In this detailed guide, we're going to walk you through the step-by-step process of packaging bottled chewing gum, from understanding regulations to the final quality check.
Importance of Proper Packaging for Retail Products
Packaging is more than just a way to store your product; it's a tool for marketing, branding, and product differentiation. It's crucial for protecting goods, but it also plays a key role in consumer safety and hygiene. For the confectionery industry, the right packaging can maintain the aroma, flavor, and texture of the product over time, which is critical for customer satisfaction.
Understanding Packaging Regulations
When it comes to packaging food products, especially those that people ingest, the regulations are strict for a reason. The FDA and other regulatory bodies set rules to ensure that packaging does not contaminate the food and keeps it safe. It's vital to stay updated with the latest guidelines to maintain compliance. This includes knowing about materials that are or are not appropriate for use with food products, as well as labeling requirements to inform consumers of nutritional information and potential allergens present in the product.
Materials Needed
The packaging process starts with gathering the correct materials. For bottled chewing gum, this typically includes the bottles themselves, caps, labels, and the outer packaging for shipping or retail display. The selection of materials is essential to maintain the quality of the product over time.
Bottle and Cap: These must be made of food-safe material, typically PET or PE for the bottle and HDPE or PP for the cap.
Labeling: High-quality labels that are resistant to moisture and oils are necessary.
💥Step-by-Step Packaging Process
Here is a detailed breakdown of the packaging process for bottled chewing gum:
1. Choosing the Right Packaging Material
The first step in the packaging process for bottled chewing gum is to choose the right packaging material. Bottles for chewing gum are typically made of plastic materials, like PET or HDPE. These packaging materials are strong, lightweight, and can be made in a range of sizes and shapes. However, the manufacturer must ensure that the packaging material is food-grade and safe for the consumer. The packaging materials should also be chosen with the environment in mind, as sustainable practices are a growing concern for consumers.
2. Screens Chewing Gum
The machine screens chewing gum that meets weight and specifications. This ensures that the product entering the filling machine is is up to standard.
3. Chewing Gum Filling
The bottle containers are filled with precisely weighed portions of chewing gum that can vary depending on the package size and the brand's formula.
4. Bottle Cap Sealing
Once the gum is placed inside the bottle, the next step is to ensure that the package is properly sealed. The sealing process is critical to maintaining the freshness and quality of the gum. The seal on the package should be airtight, preventing oxygen from seeping in and drying out the gum. Fast, efficient sealing equipment is used to complete this process quickly and accurately.
5. Adding Labeling
Bottled chewing gum needs to be labeled according to the regulatory requirements of the country it is being sold. The mandatory information includes the name of the product, the ingredients used, the manufacturing date, the expiry date, and the nutritional information.
6. Quality Check
To ensure that the bottled chewing gum meets quality standards, manufacturers conduct various tests and checks. This includes a visual inspection of the packaging, testing the seal strength, shelf-life testing, and sensory analysis. Bottled chewing gum needs to be stored in a cool and dry place to maintain its original taste. Manufacturers check the temperature and humidity levels in the storage area to maintain the product's quality.
7. Packaging
Once the quality check is done, it's time for packaging. The final step in packaging bottled chewing gum involves placing the sealed bottles into secondary packaging that can be sold in specified quantities. This packaging can take the form of boxes or cartons that hold multiple bottles of chewing gum.
8. Storage and Shipping
The final step in the packaging process is to store the packaged product in a controlled environment, away from moisture, heat, and light that can affect the shelf life and quality of the chewing gum. Proper storage is especially crucial for gum that contains high moisture levels and is sensitive to temperature changes. Once the product is ready, it is shipped to the distributor and eventually to retailers.
Conclusion
The packaging process for bottled chewing gum is a critical facet of product development and retail sales. It involves attention to both practical aspects, such as materials and equipment, and the creative side of branding and consumer appeal. With the steps provided in this guide, I'm sure you already understand the process of packaging bottled chewing gum!
Suifa news
How is Bubble Gum Made in the Factory?
2023-05-24
How Hard Candy is Made in the Factory?
2024-02-28
Get An Instant Quotation
Recommended Products
Bulk Healthy Natural Xylitol Sugar Free Tablet Chewing Gum
Detail

Checking Order

Quality Test Before Delivery

Check Items When Packing

Packaging And Transport
Send Inquiry Now!
Choose Suifa, Boost Your Candy and Gum Project!
Discover excellent gum and candy products at our factory. We create custom solutions for our customers. Join us for exclusive insights, customized products and partnerships. Leave your contact info we'll be back in touch within 12 hours!
Choose Suifa, take your bussiness to the next level!
Contact Us
WELCOME TO SUIFAFOOD YOUR TRUSTED MANUFACTURER OF GUM AND CANDY
Address: No.8 Ritian Road Songxia lndustrial AreaSonggang Nanhai, Foshan, Guangdong, China